8 Critical Questions for Selecting the Optimal Metal Seal: A Comprehensive Guide
Metal seals are critical components engineered for extreme industrial environments, including high-temperature, high-pressure, and corrosive media applications. Selecting the right metal seal is crucial for ensuring optimal performance, safety, and longevity in your specific operational context. This comprehensive guide outlines eight essential questions to consider when choosing the ideal metal seal for your industrial needs.
Understanding the Fundamental Properties of High-Performance Metal Seals
Before delving into the selection process, it's vital to grasp the general characteristics of metal seals, which are influenced by materials, geometries, and heat treatment processes:
- Dimensional Range: Outer diameters from 6mm to 4.5m
- Cross-sectional Profile: Free heights ranging from 0.9mm to 12.7mm
- Temperature Tolerance: Operational from cryogenic (-270°C) to extreme heat (+650°C)
- Pressure Capacity: Effective from ultra-high vacuum to pressures exceeding 300MPa
- Geometric Versatility: Available in circular, racetrack, oval, and custom configurations
- Sealing Efficiency: Achievable leakage rates below 1^-10 pa*m³/s
- Durability: Extended service life in demanding environments
- Material Resilience: Superior resistance to corrosion and radiation
- Structural Integrity: Immune to explosive decompression phenomena
A Systematic Approach to Metal Seal Selection
To identify the most suitable metal seal for your application, Sonkit recommends following this structured decision-making process:
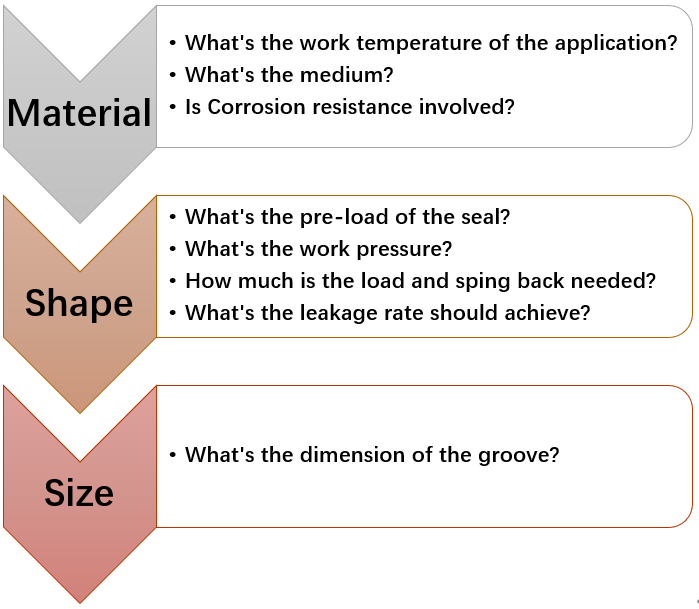
The 8 Essential Questions for Precision Metal Seal Selection
When selecting a metal seal, it's crucial to consider three primary aspects: Material, Geometry, and Dimensions. Here are the eight critical questions that will guide you to the optimal sealing solution:
Material Selection Criteria:
- Temperature Range: What are the minimum and maximum operating temperatures in your application?
- Media Compatibility: What specific fluids or gases will the seal encounter during operation?
- Corrosion Resistance: Are there particular corrosive elements or environments the seal must withstand?
Geometry Selection Parameters:
- Pre-load Requirements: What is the necessary initial compression force for effective sealing?
- Pressure Conditions: What are the minimum and maximum working pressures the seal must accommodate?
- Load and Resilience: What specific load-bearing capacity and spring-back characteristics are required?
- Leakage Tolerance: What is the maximum acceptable leakage rate for your system?
Dimensional Considerations:
- Groove Specifications: What are the precise dimensions of the sealing groove or cavity?
Sonkit's Advanced Metal Seal Portfolio: Tailored Solutions for Diverse Applications
Sonkit offers a comprehensive range of metal seal types, each engineered for specific operational requirements:
- Metal O-Rings: Cost-effective solution for high-load, high-pressure scenarios
- Metal C-Rings: Popular design offering superior leakage control and excellent resilience
- Spring-Energized C-Rings: Enhanced variant providing increased load capacity and improved sealing performance
- JCE (Jacket C-Ring External): Specialized design featuring an aluminum layer for specific application requirements
- E-Rings: Engineered to deliver maximum spring-back among all metal seal configurations
- V-Rings: Versatile, low-load seals widely utilized in valve applications
- COI/COE (Metal Commaseal): Designed for both internal and external pressure applications

Conclusion: Ensuring Optimal Sealing Performance Through Informed Selection
By thoroughly addressing these eight critical questions and carefully evaluating the material, geometric, and dimensional aspects, you can confidently select a metal seal that precisely meets your application's unique requirements. This comprehensive approach ensures superior sealing performance, extended operational lifespan, and enhanced system reliability across a wide range of industrial applications.