Metal Seal Best Practices: Optimizing Performance in Extreme Industrial Environments
In today's advanced industrial landscape, applications increasingly demand sealing solutions capable of withstanding extreme conditions, including high temperatures, elevated pressures, and vacuum environments. Metal seals have emerged as the premier choice for these challenging scenarios. This comprehensive guide explores the best practices for implementing metal seals, providing engineers and technical professionals with essential insights into their mechanisms, advantages, and optimal application strategies.
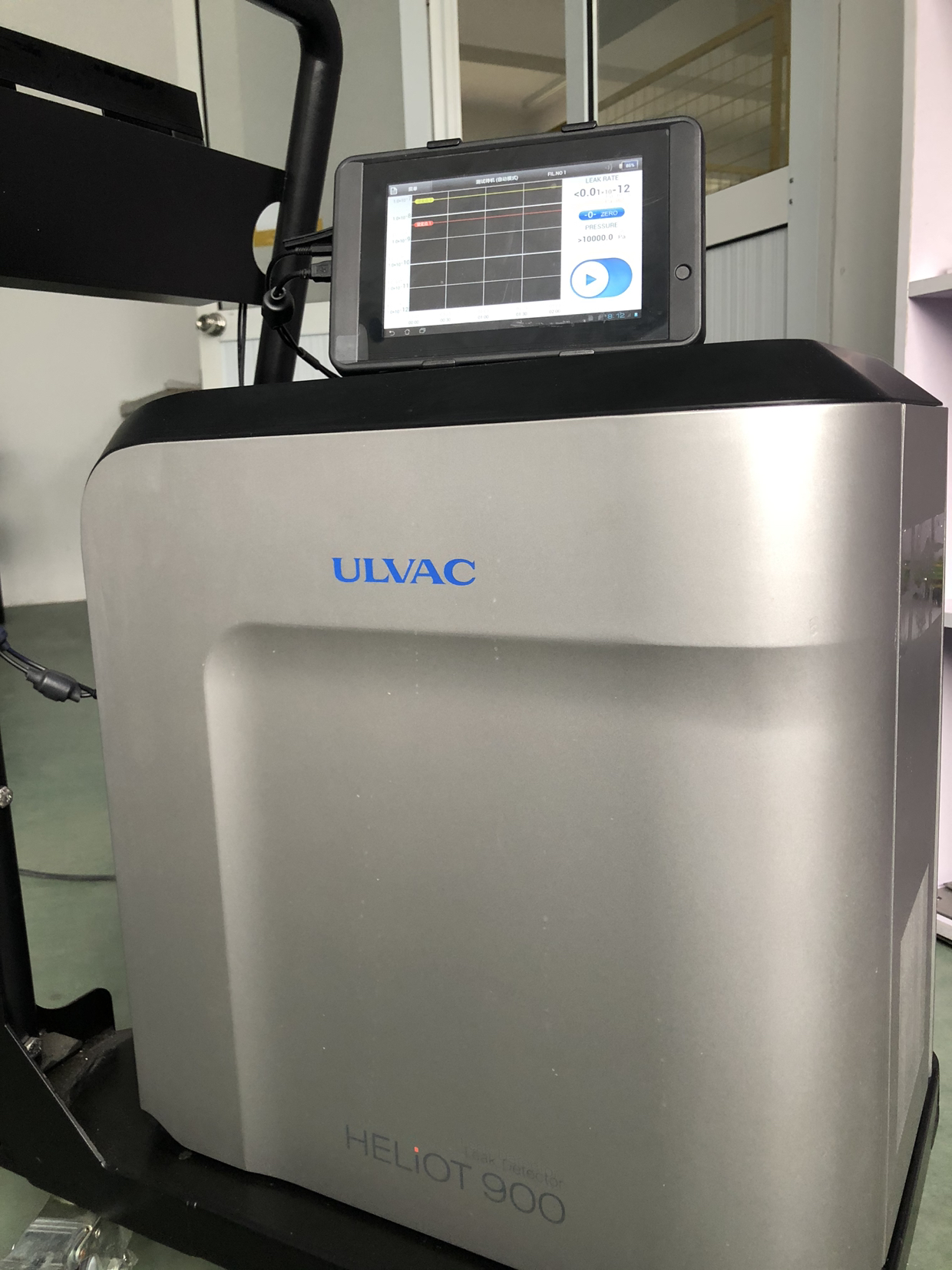
Leveraging Metal Seals in High-Temperature Applications
Unlike conventional polymer or PTFE seals, metal seals are engineered from high-performance alloys, such as Inconel 718, capable of maintaining integrity at temperatures up to 650°C and beyond. This exceptional thermal resistance makes them indispensable in applications where standard sealing materials would fail. Consider the following temperature capabilities of common metal seal materials:
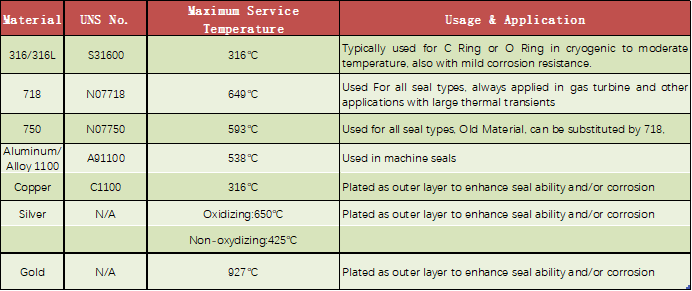
Superiority of Metal Seals in Vacuum and Cryogenic Environments
In applications involving extreme low temperatures or vacuum conditions, metal seals demonstrate significant advantages over polymer alternatives. Their ability to maintain elasticity and resist embrittlement at cryogenic temperatures ensures consistent sealing performance where other materials would fail. This characteristic is particularly crucial in aerospace, semiconductor manufacturing, and scientific research equipment.
High-Pressure Applications: The Metal Seal Advantage
Metal seals excel in static applications with pressures reaching up to 500 MPa (72,500 psi). A key principle in high-pressure sealing is that increased seating load correlates directly with improved sealing effectiveness. This relationship allows metal seals to maintain integrity under extreme pressure conditions that would compromise traditional sealing solutions.
Corrosion Resistance: A Critical Asset in Harsh Environments
The inherent properties of high-performance metal alloys used in sealing applications provide exceptional resistance to corrosive chemicals and intense radiation. This resistance far surpasses that of rubber or other traditional sealing products. When combined with appropriate material selection and surface treatments, metal seals offer unparalleled durability and longevity in the most aggressive industrial environments.
Optimizing Sealing Effectiveness Through Surface Engineering
A critical factor in maximizing the performance of metal seals is the surface finish of both the seal and the mating hardware. Advanced coating technologies can significantly enhance sealing effectiveness, especially in applications where achieving an ideal surface finish on mating components is challenging. The following illustration demonstrates how specialized coatings improve sealing by conforming to surface irregularities:
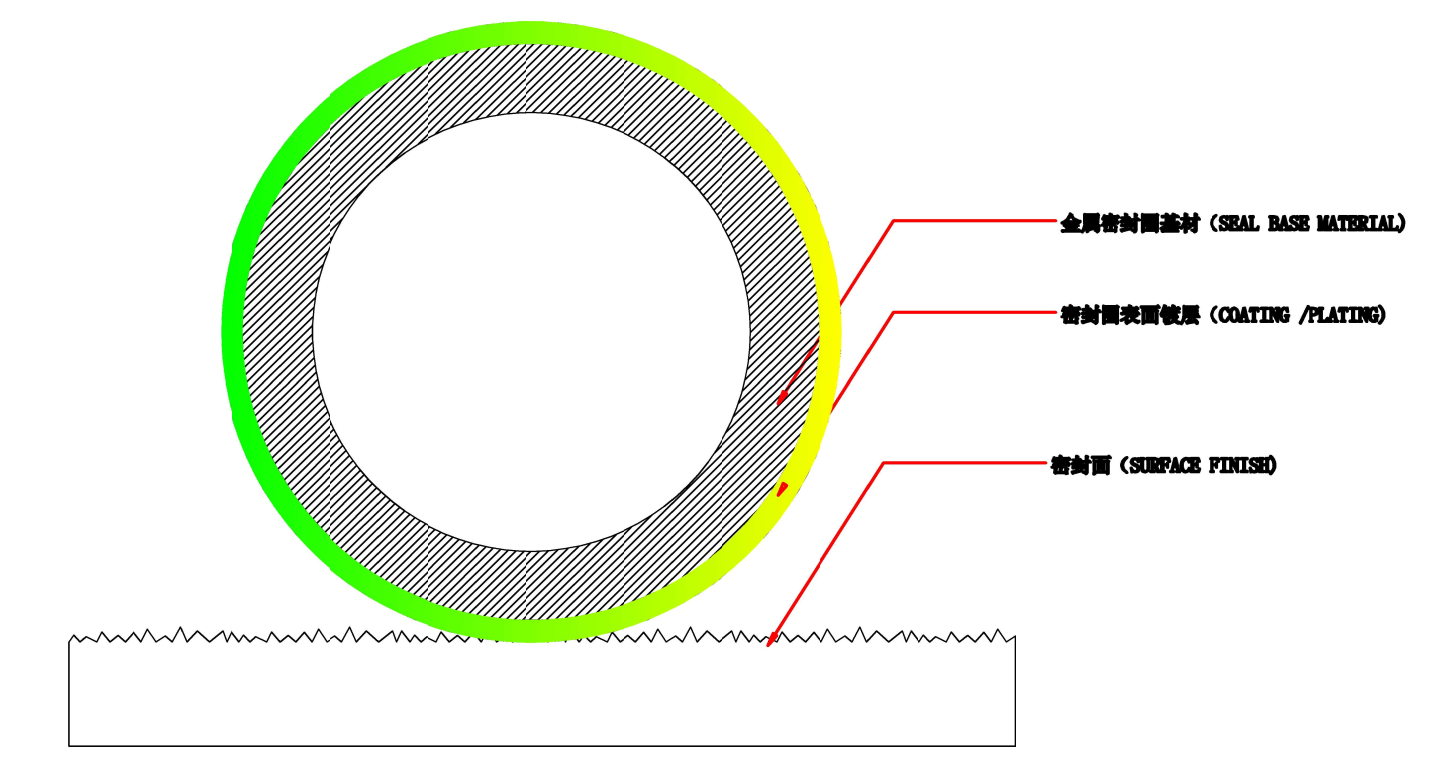
Key Performance Attributes of Advanced Metal Seals
- Extreme Temperature Tolerance: Operational from cryogenic (-270°C) to high-temperature (+650°C) environments
- Broad Pressure Range Capability: Effective from ultra-high vacuum to extreme pressures (+500 MPa)
- Versatile Geometries: Available in circular, racetrack, oval, and custom configurations to meet specific application requirements
- Ultra-Low Leakage Rates: Achievable rates below 10^-10 pa*m³/s, ensuring hermetic sealing in critical applications
- Extended Operational Lifespan: Significantly outlasts traditional sealing materials in extreme conditions
- Superior Chemical and Radiation Resistance: Maintains integrity in the presence of aggressive media and high-radiation environments
- Resistance to Explosive Decompression: Crucial for high-pressure gas applications where rapid depressurization may occur
Sonkit Industry: Pioneering Advanced Metal Seal Solutions
Sonkit Industry has established itself as a leader in metal seal technology, providing cutting-edge solutions across a diverse range of high-demand sectors, including:
- Nuclear Power Generation: Containment systems and reactor components
- Aerospace and Defense: Propulsion systems and high-altitude equipment
- Advanced Manufacturing: Mold hot runners and high-precision tooling
- Petrochemical Processing: High-pressure reactors and transport systems
- Semiconductor Fabrication: Ultra-high vacuum chambers and gas delivery systems
- Energy Production: Gas turbines and geothermal power systems
- Oil and Gas Exploration: Subsea equipment and high-pressure wellheads
With a track record of serving over 2,000 global clients, including numerous Fortune 500 companies, Sonkit's metal seal products have consistently garnered acclaim for their exceptional quality, reliability, and performance in the most demanding industrial applications.